In warehouse operations, ensuring that pallets are properly placed within racking systems is a key component of safety and efficiency. While it may seem like a minor detail, the positioning of each pallet can prevent damage, reduce safety risks, and streamline forklift operations.
Here’s why correct pallet placement matters and what to keep in mind when handling pallets in racking systems.
Why Pallet Placement Matters
Racking systems are designed with specific tolerances to safely support the weight and size of the pallets they hold. Pallet racking is designed to be loaded upon in a uniformly distributed manner, by having pallets incorrectly sited within racking they would not be being used as designed and specified by the racking manufacturer.
In line with SEMA (Storage equipment manufacturers association) guidelines, pallets should have a recommended overhang front to back of 50mm protruding the beam front face, and the same at the rear.
Pallet racking is designed to have a minimum clearance in back to back racking of 100mm between pallets, this is often referred to as the flue. With pallets being loaded incorrectly into the system, it can result in the 100mm gap between pallets being less or in some cases pallets touching. This practice can result in:
- Damage to the Racking System: Misaligned pallets can cause structural damage to components like uprights, beam connectors, and frame braces. Over time, these damages compromise the integrity of the racking, increasing the risk of collapse.
- Improved Forklift Operation: Adequate clearances make it easier for forklift operators to position pallets safely without risking damage to the racking or pallets.
- Maintaining Load Balance and Safety: When pallets overhang the beams correctly (by approximately 50mm at the front and rear), they are better supported and distribute their load more evenly. This prevents the pallet from slipping or tipping, minimizing accidents.
- Pallets becoming dislodged: Without the correct clearances being in place there is a risk that as pallets are loaded/unloaded from the system, pallets may become dislodged, falling through the beams in most cases. From experience and dependant on the product being stored, this can have disastrous consequences for personnel within the area & racking damages.
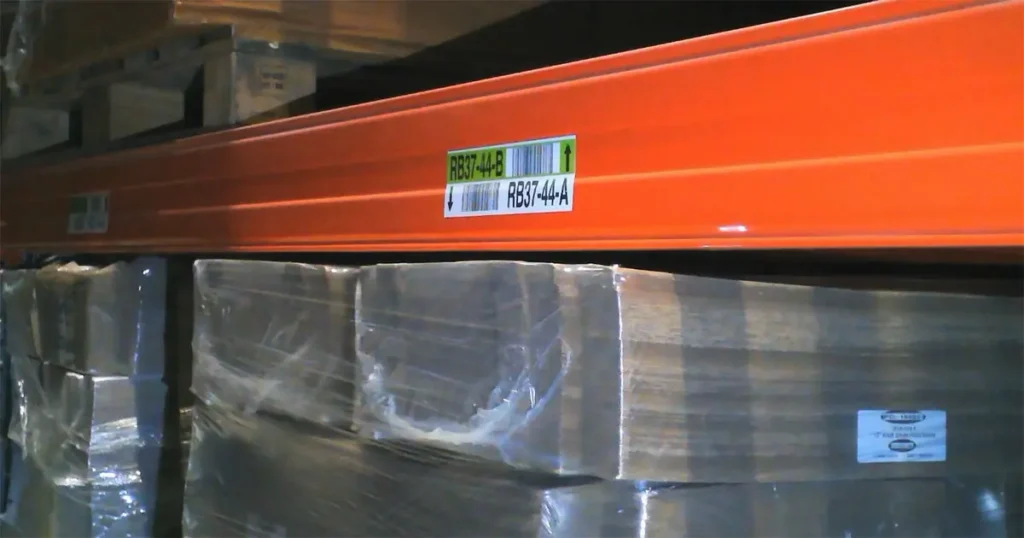
The way in which pallets are designed is that the pallet corner blocks are the weight bearing component of the loads being imposed. The pallet stringer boards are in place to tie the pallet together and offer a good overall structure to carry loads of various weights and sizes.
By operating to the designed 50mm overhang front to back within racks this will ensure that the load sits directly upon the racking beams at its strongest point, on the pallet corner blocks. Where pallets are too large for the system or incorrectly placed upon beams, it is likely they will have the overall weight imposed upon their stringers (underside slats) of which are likely to deflect and damage, in some cases resulting in pallet failures.
Get a Quote
With over 30 years of experience our fully SEMA approved inspectors offer nationwide racking inspection and training.
Recommended Pallet Clearances – Around the pallets
The below diagram explains the SEMA guidelines on pallet clearances around the pallets and pallet loads. As racking heights increase, pallet clearances must also be increased to ensure additional control measures are in place to account for the additional height and in turn reduced visibility in many cases.
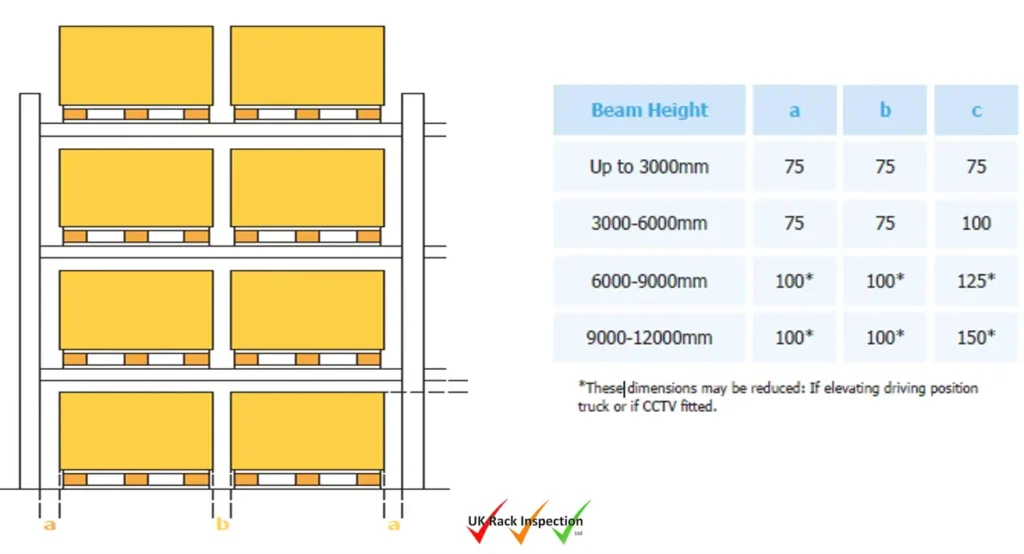
Best Practices for Pallet Placement in Racks
To ensure safety and avoid unnecessary damage, here are some best practices:
- Adhere to Overhang Guidelines: Ensure that pallets have a 50mm overhang at both the front and back of the racking beams. This overhang enhances stability and maintains the intended load distribution.
- Train Forklift Operators on Correct Placement: Take the time to train forklift operators on these guidelines. Awareness of correct placement techniques and the reasoning behind them will help avoid damage and improve warehouse efficiency.
- Regularly Inspect Racking for Damage: Implement regular inspections to check for signs of wear and tear, such as bent beams or split connectors. Promptly addressing any issues prevents them from becoming more severe.
- Conduct daily aisle pallet placement checks: A daily pallet placement check could be undertaken to ensure pallets are correctly seated within the racking bays. This could be a similar check to the MHE daily check carried out on site and would ensure that any pallets found to be incorrectly placed are rectified before the logistical operations begin.
- Monitor and Adjust Racking Configurations: If your warehouse handles various pallet sizes, ensure your racking setup can accommodate them properly. Adjusting configurations based on load requirements can prevent misuse of racking components. It should be mentioned that any racking alterations should be undertaken by a certified & competent person and load notice suppliers must be consulted before any works are undertaken. If you are unsure, please feel free to get in touch for more information and guidance.
A Few Seconds That Make a Big Difference
Taking a few extra moments to ensure pallets are positioned correctly can significantly reduce the risks associated with improper pallet placement. By maintaining clearances, avoiding flush loading, and training operators, warehouses can improve the longevity of their racking systems, prevent accidents, and streamline daily operations.
For a safer and more efficient warehouse, let’s give proper pallet placement the attention it deserves.
To equip your on site personnel with the knowledge and skills to conduct internal inspections, get in touch and booked onto our ‘360’ racking compliance course.
Get a Quote
With over 30 years of experience our fully SEMA approved inspectors offer nationwide racking inspection and training.