Racking Component Breakdown & Their Structural Importance
Racking structures have been designed and rigorously tested to be able to withstand loads imposed on them during the day-to-day use, each component is designed specifically to maintain the rack load bearing and structural stability, each individual component is vital in ensuring the performance and safety.
Here we will briefly explain the main components with our racking component breakdown & their structural importance guide.
Racking Frames
Racking frames are constructed with front & rear uprights, with a baseplate on the foot of each section offering stability, weight transfer to the floor slab & enables a fixing to the floor slab below keeping the rack mechanically fixed in place. The rack uprights are joined together by frame braces of which add the rigidity to load bear when connected by beams to form a bay of racking. Racking frames come in various depths from around 400mm deep up to 3000mm deep racking bays, although the most common sizes are 900mm & 1100mm deep racking frames.
The depth of the frame is dictated by your pallet depth.



Racking Uprights
A cold formed steel section specifically designed for load bearing in a downwards force.
Each manufacturer has dedicated designs to suit varying carrying capacities (called ‘Duty’) generally stamped in the front or side face. On any racking installation your racking installer/manufacturer should carefully assess your maximum bay & beam loads to ensure the rack uprights have the correct carrying capacity for site requirements.
Generally, slots in the front face to seat the beams but louvres are also used.
Racking Frame bracings
Racking frame bracings are typically bolted (may be welded) to the front and rear upright. They ensure the ‘frame’ is both square and rigid, whilst also assisting in transferring load to ground level as well as ‘some’ impact resistance.
Frame bracing damages at lower levels are generally more critical than those at higher levels due to the increased pressures from the loadings above, however both do play an essential role in any warehouse racking system.

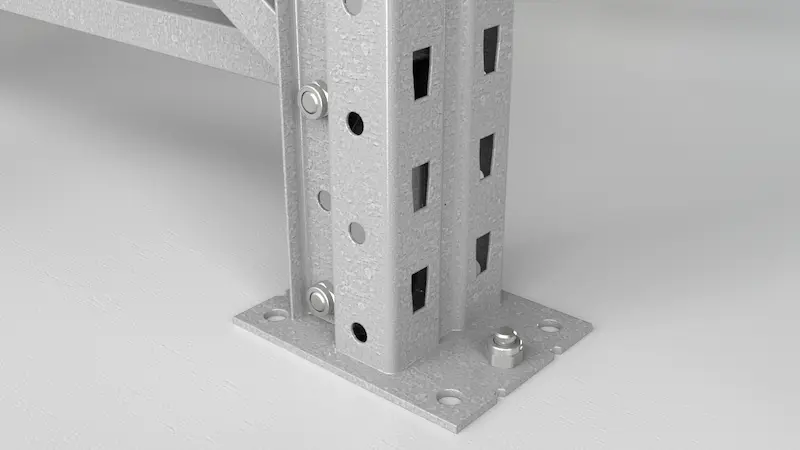
Rack Baseplates
Baseplates seat uprights solidly on the ground to offer positive support enabling the transfer of load from the upright to the floor slab. Baseplates are either welded or bolted to upright sections and should be fixed to the floor slab with a minimum of 1 floor fixing per racking baseplate however by design this may be more.
Baseplates can vary depending on their application. With multiple systems such as VNA racking & drive in racks they are specified by manufacturer to ensure the best & most suitable compatability for their use.
Baseplate damages should result in replacement as they have such importance with rack stability and load transfer of the entire rack loadings above.
Racking Floor fixings
Floor fixings have an essential role in any warehouse racking system, assisting with structural stability and load bearing of the racking structure. In most cases a single fixing is used (despite alternative holes in the baseplate) but by design there maybe 2 or more floor fixings required.
Each floor fixing is specified to be able to transfer 5Kn in shear and 3Kn in tension.


Racking Beams
Racking beams are the horizontal bar that the pallets sit on, slotted into the face of the upright. They come in many different dimensions to suit the pallet weights in use within the racking system and the span required to suit the pallets in use.
Beams generally come in open section or a box section beam, however may be a section of RSJ. The most common size for racking beams is 2700mm or 3300mm but can go up to any length designed by the racking manufacturer.
Beams are designed and tested to carry varying loads, manufactured in different sections to suit requirements, not every beam is rated at 2000Kg!
Racking Beam Safety Locks
Beam safety locks are possibly the lowest cost value item in the warehouse racking system, but no less important. Beam Safety Locks ensure that the beam is located correctly in the upright, also it reduces the chance of beam becoming dislodged if subjected to a small uplift force during day-to-day operations.
Beam safety locks may be a plastic type such as Apex beam safety locks or mostly found to be of a metal design with their own distinctive design pattern.
As beam safety locks are manufacturer specific it is important that the correct beam safety lock is fitted, one at each end of the beam. If you get stuck feel free to send us an image of your racking system and we will assist.

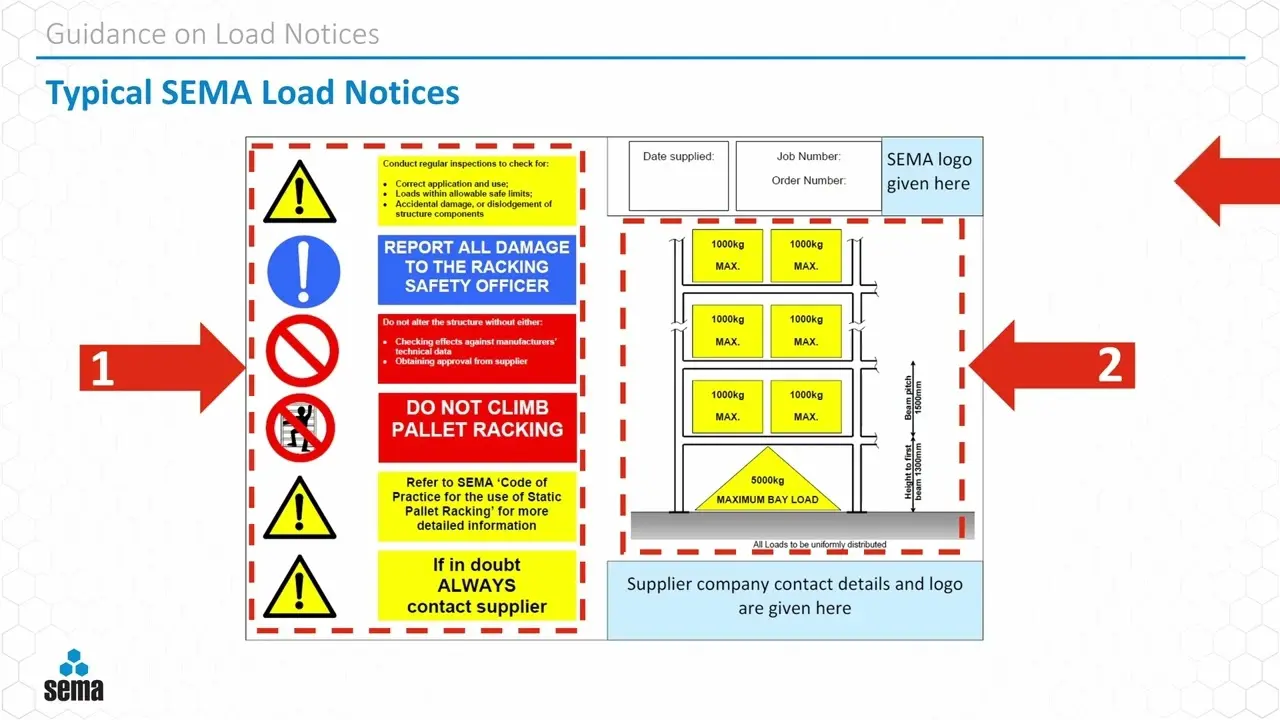
Racking Load Notices/SWL Notices
The SEMA load notice is a key piece of information relating to the individual racking structure, it gives general Health & Safety information including warnings, but more importantly, shows manufacture information of loadings and design details at the original time of installation.
Load notices displayed on racking after 2012 should be displaying height to first beam, beam pitch, beam load, bay load, date, reference number and the traceability information of the company that provided the notices.
Should for any reason the rack be re-configured, the racking load notice MUST be updated to reflect the new layout with original manufactures data.
Load notices should be displayed on all storage equipment, so whether you have a single shelving bay or a mezzanine floor, safe working load notices should always be displayed.
Rack Protection
Racking protection is a retrofit option in various forms designed to offer protection to the uprights and/or end frames. Racking protection within aisles should be regarded as a ‘last resort’ means of avoiding damage and other ‘Root Cause’ methods of damage prevention should be considered before taking the decision to use rack protectors.
However, as advised within the Health and safety executive (HSE) extract – HSG76 Warehousing and storage a guide to health and safety – Racking protection should be in place at aisle ends and transfer bays (tunnel bays) to ensure end frames are sufficiently protected.
Where goods are stored against end racking frames it is advised that low level full height rack frame protection be in place to assist in the prevention of goods or mhe forks causing damages to end frame components.

SEMA Damage Classifications
Under SEMA Standards and Guidelines and EN15635 damage limits of components have been adopted since the mid 80’s with colour coded risk classification categories to reflect the seriousness of issues and the response required.
Red Risk
Very serious damage requiring immediate action. Areas where a high level of damage is identified of over twice the SEMA limits. This warrants immediate offloading and isolation of the affected area until repair work is carried out.
Amber Risk
Hazardous damage requiring action as soon as possible. Areas where the damage identified is greater than the SEMA limits. This warrants remedial work to be carried out. However, the damage is not sufficiently severe to warrant the immediate offloading of the area.
No additional loads shall be placed in the affected area and, once the pallet positions in this area are emptied, they should not be refilled until the repairs are carried out. If repairs are not carried out within 4 weeks, an Amber risk item automatically becomes a RED RISK item.
Green Risk
Damage requiring surveillance. Areas where damage is present, however, the level of damage is within the SEMA limits and should be recorded for further consideration at the next inspection.
Any damage will result in a reduced safety factor in the structure and deviations in excess of the SEMA limits should result in the affected area of the racking being offloaded. The course of action following categorization is shown in the following flow chart.