SEMA Approved Cantilever racking Inspectors
Expert Cantilever Racking Inspections
With UK-wide coverage & extensive experience and knowledge of cantilever-racking
Our SEMA-approved Cantilever racking inspectors keep your site safe and compliant with HSE & PUWER regulations.
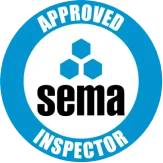
Meet & Maintain Cantilever Racking Compliance In Line With HSE, SEMA And Auditor Requirements & Regulations.
Our Cantilever Rack Inspections Ensure Compliance & Safety For Your Site.
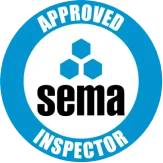
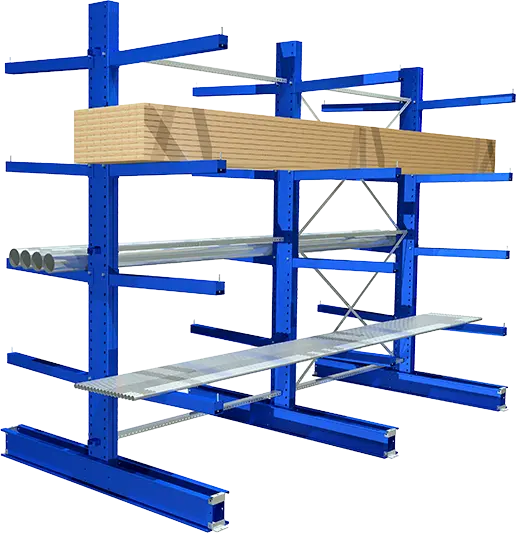
Cantilever racks are often used for heavier and longer loads than standard pallet racking. Their uses are widely used for sheet storage or long items that cannot be loaded into standard pallet racking.
With larger loads in use, the risk and severity of Cantilever racking damages increases. By having your Cantilever racking inspection undertaken by our SEMA approved Cantilever inspectors, we will ensure that you are made aware of any potential issues. Our racking inspector will assess the racks in detail keeping you both safe and compliant. Our experience enables us to be able to offer preventative damage techniques , saving your business from having downtime and loss of revenue.
The Importance of Having Your Cantilever Rack Inspection
- Annual Inspections: A strongly advised requirement under HSG76 and PUWER, annual inspections ensure your racking remains safe and compliant.
- Minimize Downtime: Detect and address issues early to avoid costly disruptions.
- Protect Your Workforce: Maintain a safe working environment and reduce the risk of accidents.
Why Choose Us?
- Nationwide Coverage: We serve businesses across the UK.
- Experienced Inspectors: Our team has extensive knowledge of leading racking brands, including Stakapal, Wickens, Space Productiv, Prodek, and Ohra.
- SEMA Approved Inspector Accreditation: Inspections conducted to the highest industry standards.
- Custom Solutions: Services tailored to your specific racking systems and operational needs.
What to expect from your cantilever racking inspection:
- Following each inspection Cantilever racking inspection you will receive a detailed report with clear recommendations to address any identified risks. Our in depth Cantilever racking audit will include but not be limited to:
- Cantilever column conditions & structural integrity
- Cantilever arms for damages, twisting & arm levels ensuring they have not dropped below horizontal
- Bracing gate & horizontal bracing conditions, ensuring the system is able to maintain rigidity
- Cantilever bases are in a good condition to enable the racks to be sufficiently supported
- Arm retention is suitable for continued use (Arm pins, bolts or connectors to columns)
- Floor fixing bolts are sufficient & secure, keeping your system fully grounded as intended
- Load suitability, load clearances & damage prevention techniques and recommendations, ensuring your Cantilever rack system remains safe, compliant & a vital asset to your business
- Ground suitability for the even weight distribution of the racks and the safe operation for MHE operatives.
- Cantilever racking safe working loads are displayed and correct for the racking current configurations
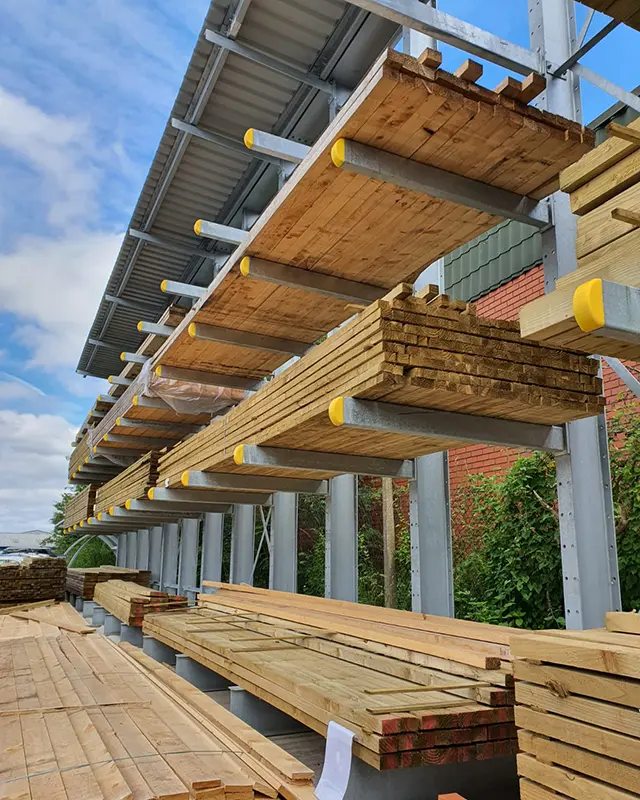

Customers We Have Carried Out Inspections For




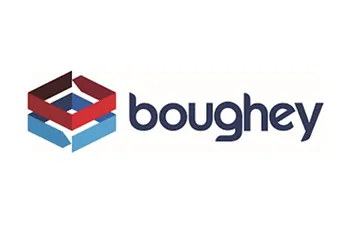



















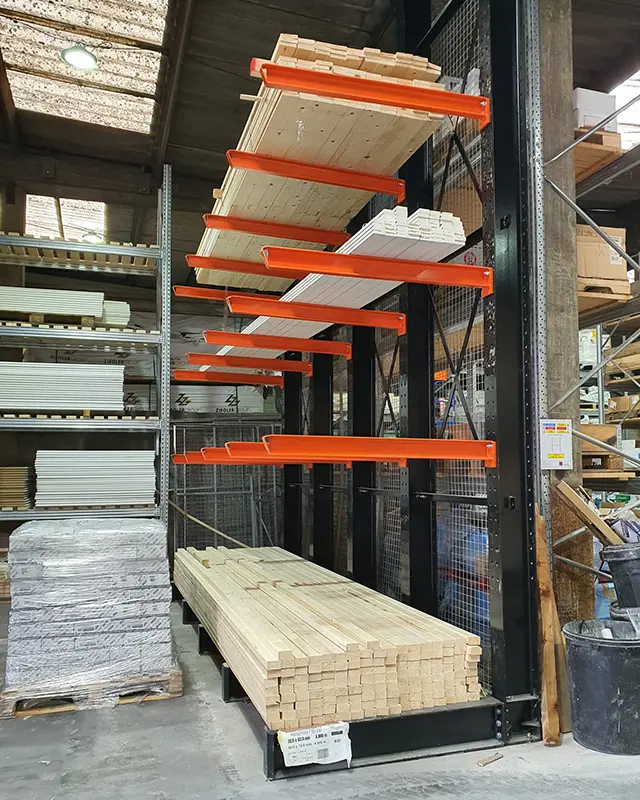
Cantilever Racking Inspection Training
Equip your team with the skills to perform regular, in-house Cantilever racking inspections with our tailored Cantilever rack Inspection Training Courses. Designed to meet industry standards, these courses ensure your team understands the essentials of safe cantilever racking operation and maintenance.
What the Training Covers:
- Overview of cantilever racking design and load-bearing principles.
- Identify faults and damage indicators in line with SEMA damage classifications.
- Performing routine in-house inspections in line with SEMA, HSG76 and PUWER REGULATIONS.
- Practical exercises for real-world application.
- Health and safety practices & regulations.
- Essential Cantilever racks inspection checklist & required inspection tools
- Tailored for your site requirements
- Upon successful completion, delegates will be certified for 3 years to undertake your in-house PRRS (person responsible for rack safety) regular racking inspections
All Cantilever racking training sessions are delivered by our experienced and trained professionals who combine technical expertise with hands-on knowledge.
Rack Inspection Reviews
Racking Manufacturers We Commonly Inspect

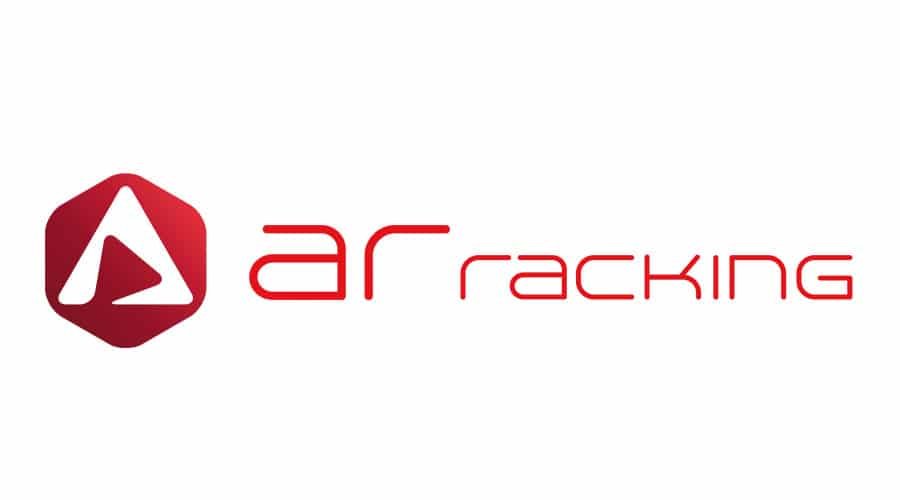

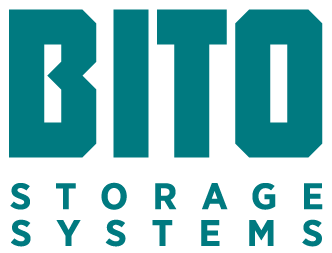
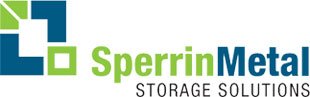



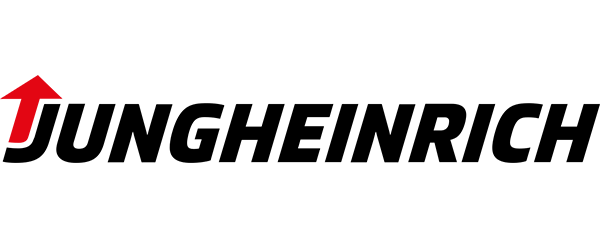
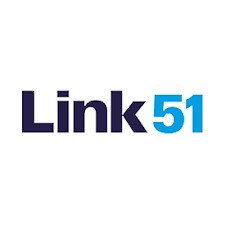
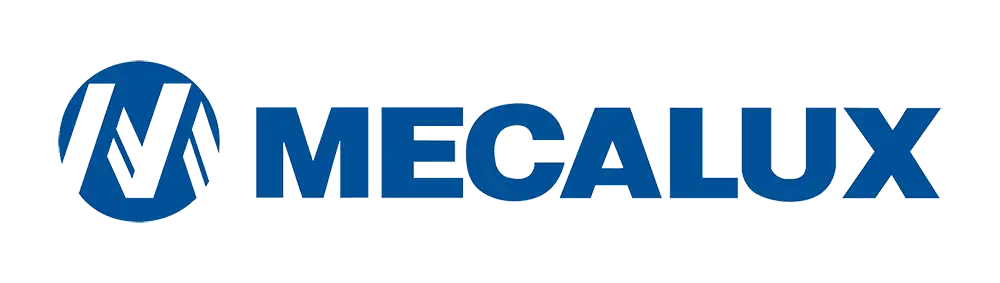
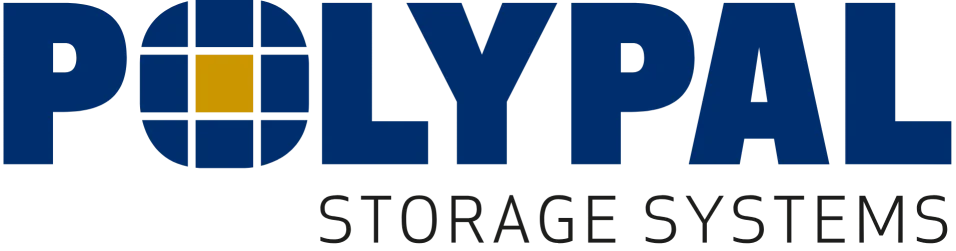

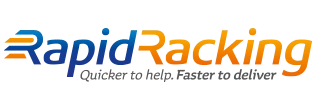



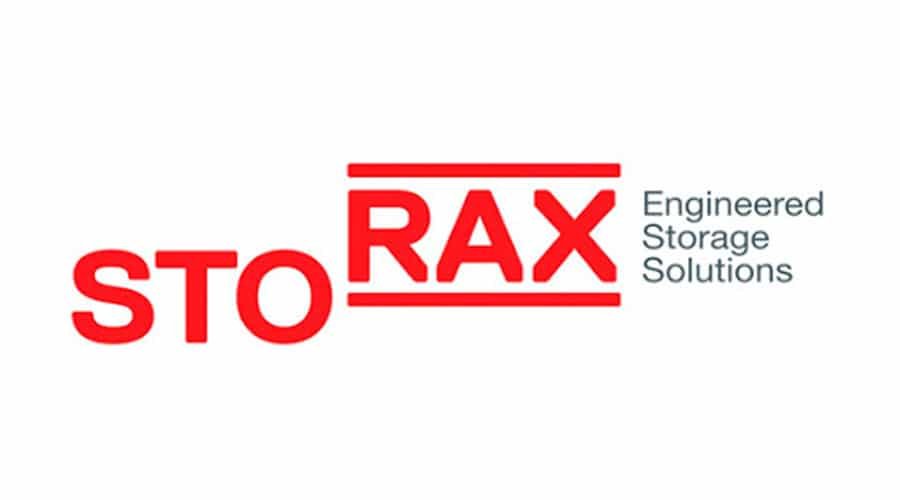



Frequently Asked Questions
Why do I need to have a racking inspection?
Racking and storage equipment falls under PUWER (provision and use of work equipment regulations) and is advised to be checked at least annually within by a technically competent person of which a SEMA approved inspector satisfies this requirement. HSE documentation also relating to the recommendation to have an annual professional racking inspection is:
- HSG76 – Warehousing and storage – A guide to health and safety
- Workplace health, safety and welfare regulations 1992
An annual racking inspection will ensure that your racking has been installed to manufacturer specifications, has plausible weight loading information displayed, is correct and being used correctly for its current application and that it is in a good serviceable condition.
What are the benefits of using a SEMA approved inspector?
- We will ensure compatibility and suitability of your storage equipment
- Fully Approved Inspectors as recognised by the HSE
- We Carry out an in depth inspection process in order to provide you with a fully detailed report with locations and remedial actions listed
- Enable you to achieve and maintain compliance with regards to Health and safety legislations & PUWER regulations.
- Check that your racking installation has been installed to manufacturer specifications
- Ensure load notices are in line and relevant to the racking current configurations
- Offer guidance on areas that may be showing signs of repetitive damages, capturing areas before damages requiring replacement components
- Assess the pallet and pallet load suitability on site
- Offer guidance on rack related health and safety issues, keeping you up to date with regulations
- Give an in depth specification of the storage equipment
- Full client debrief following the inspection where recordings can be found and guidance given
Aren’t all racking inspectors SEMA approved anyway?
The answer is no.
Our advice is to always ask for the inspectors SARI number of which is an individual identification number assigned to each SEMA approved inspector, this should be identifiable on your racking inspection report also.
Furthermore, there are PUWER racking inspectors offering a damage report only style of report. Our concern with this type of inspection is a questionable compliance and that vital installation or health and safety issues would likely not be identified.
Our view is that if you are looking for a racking inspector why would you not want a full audit from a qualified inspector opposed to a brief overview.
Should a racking inspection be carried out annually only?
A racking inspection should be undertaken on an annual basis, when racks have been moved, or reconfigured.
Should repairs or installations be undertaken by a none SEMA approved installer (SIERS) it is advised that an inspection be carried out before the system is used to ensure it has been built or repaired to standard.
In house inspections should also be carried out by trained personnel at regular intervals throughout the year in between annual professional inspections.
The personnel should attend a racking awareness course and have a certified level of competence, they may then undertake your internal inspections of which should be recorded to satisfy auditor and HSE requirements.
Will any guidance or assistance be given after the inspection?
We strive to offer a great aftercare service to our customers and in doing so have built relationships up and down the country.
We are always on hand to offer help and guidance to ensure you are always one step ahead of all things rack related.
Although we work as a fully independent inspection company we do have highly recommended contacts within the storage industry of whom are all certified SEMA members offering repairs and installations.
This information can be given should you request any repairs or installations after your inspection.
Why should I use UK rack inspection for my annual racking inspection?
The UK rack inspection team have been in the storage industry for over 30 years, building expertise, knowledge and assisting customers across the UK. We then looked to build something of our own to be able to offer a next level service we feel is vital for our customers. Our experience has enabled us to have an insight as to what we must do to be the best we possibly can.
We are and we will:
- Accredited In House SEMA Approved Inspectors (SARI)
- Offer clear and concise reporting to customers
- Communicate any immediate actionable findings whilst leaving a RED risk report with our site contact when required
- Independent SEMA Inspectors to prevent conflict of interest
- Inspect to detailed SEMA standards
- Offer damage prevention recommendations where necessary
- Ensure racking has been installed and is being used to manufacturer specifications and recommendations
- Be on hand for any assistance required after the inspection has been submitted